Infrared Thermography:
Allis Engineering has been providing comprehensive Infrared Thermographic services nationwide for over 20 years. All inspections are performed by our own certified thermographers, not sub-contractors. Allis Engineering complies with NFPA 70e while conducting the infrared inspection. Detailed and thorough reports are accessible via the web.
Why use Infrared Thermography?
If you are a facility manager, maintenance manager or building owner responsible for safety, production and repair at your facility, you cannot afford to be without a regular infrared (IR) thermographic survey of your electrical system. An Infrared electrical/mechanical inspection is the most cost effective method of predictive maintenance that can be performed. Infrared inspections can quickly and efficiently find areas that are most in need of your maintenance dollar. Finding problems at an early stage allows repairs to be made before causing serious failure or costly damage and down-time. Infrared Inspections have been proven to provide a 4:1 ROI.
What should be inspected?
Your entire electrical system: panels, sub-panels, motor control centers, disconnects, distribution centers, switchgear, transformers, bus ducts, ATS’s and VFD’s.
What is an Infrared Electrical Inspection?
An Electrical Infrared Inspection uses an Infrared Imaging device (camera) to locate potential electrical issues that would otherwise be invisible to the naked eye.
Infrared Inspections can help locate: loose connections, loose fuse clip assemblies, overloaded circuits, and faulty breakers, loose or faulty disconnect knife switches, phase imbalance, faulty bus connections, etc., etc.
Infrared imaging can be successfully applied to the following types of solutions:
Preventative Maintenance – scan electrical and mechanical equipment for trouble spots so they can be repaired before failure.
Predictive Maintenance – monitor limited life components to predict and schedule replacement before failure.
Electrical Inspection – find problems caused by overload and high resistance.
Steam Trap Analysis – locate plugged or leaking steam traps that are not visible to the human eye.
Roof Moisture Analysis – pinpoint leaks for repair, saving thousands of dollars on roof replacement.
Building Heat Loss Analysis – find damaged, missing or deteriorating insulation in walls, windows and roofs that cause heat/energy loss.
Research and Development – discover the heat flow properties of new products or processes.
Acceptance Testing and Quality Control – scan new equipment to find faults or defective workmanship.
Digital to Thermal
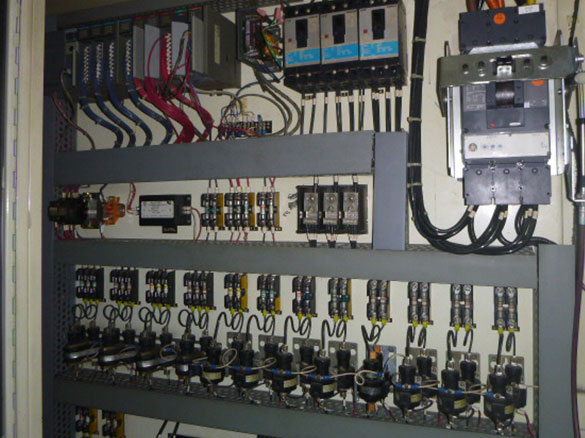
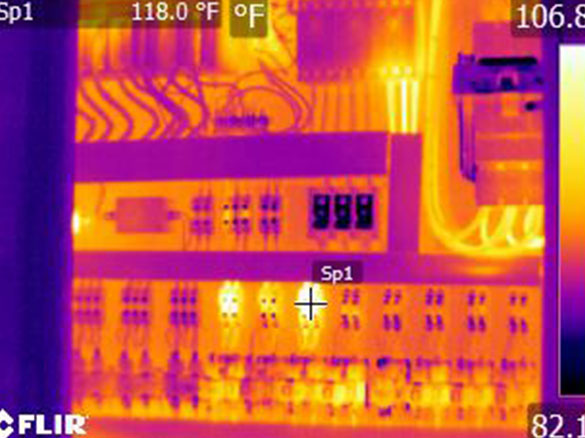
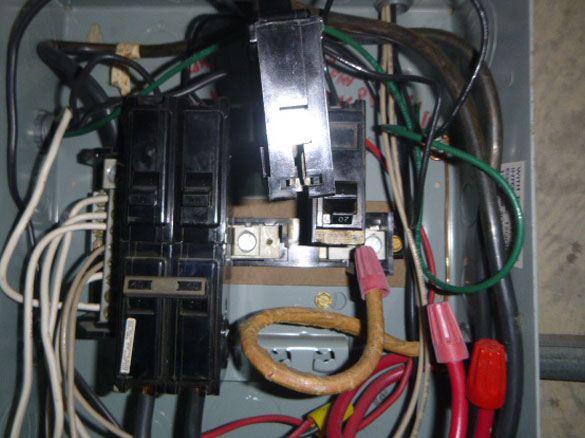
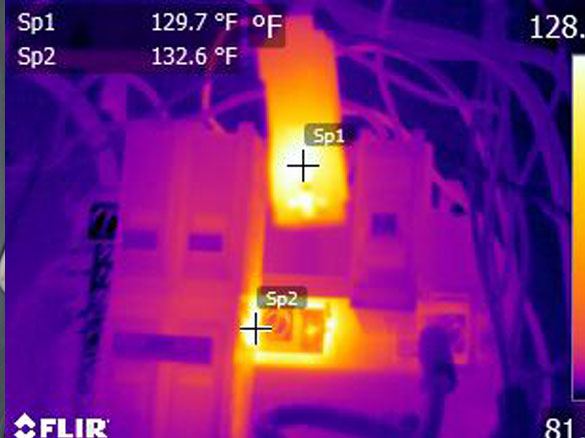
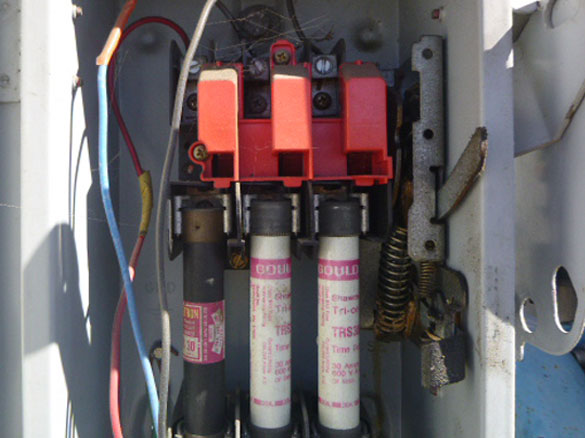
